Nanocomposites
04. Covalent organic frameworks based nanocomposites
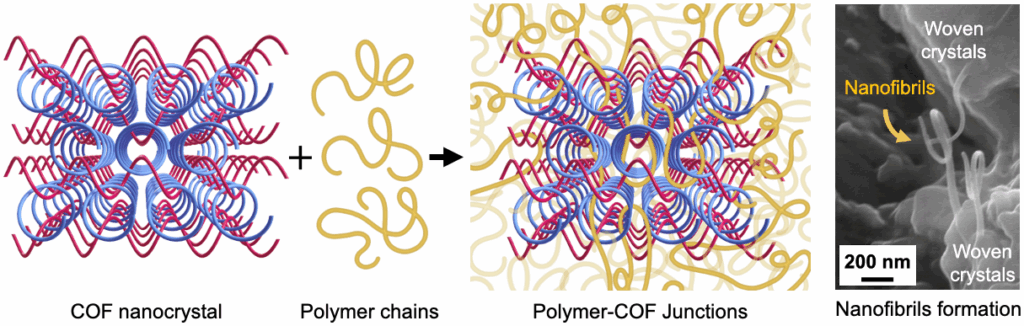
3D woven covalent organic frameworks (COFs) template polymer chains, forming entangled junctions that facilitate nanofibril formation under stress. In this study, we used various types of COFs as nanofillers and embedded them into a polymeric matrix to achieve mechanically reinforced nanocomposites, which can improve stiffness, strength, and toughness simultaneously—properties that are mutually exclusive.
- Keywords: covalent organic frameworks, nanocomposites, polymer-COF junctions, mechanical properties
03. Materials characterizations (mechanical, thermal, chemical, etc.)
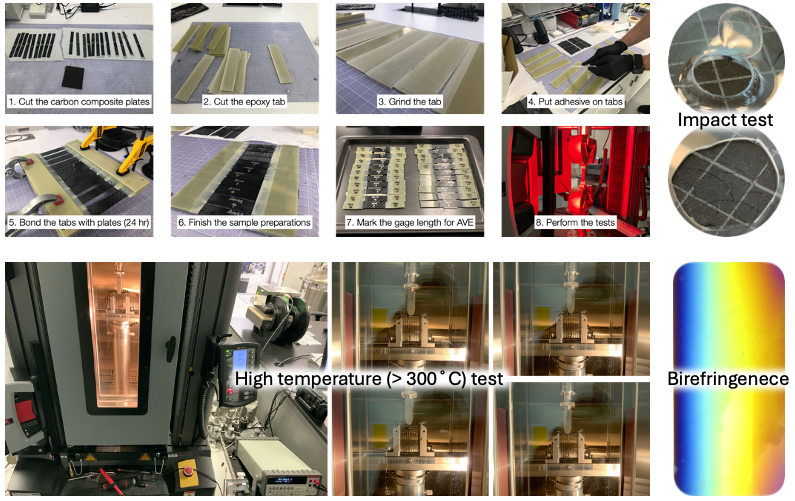
We focus on comprehensive analysis, modeling, and applications of physical properties of polymers and composites used in industry. Synthesizing polymers, we conduct and analyze tests ranging from mechanical properties—such as quasi-static tensile, bending, torsion testing, high-speed impact tests, dynamic mechanical analysis (DMA), and rheology—to physiochemical properties through differential scanning calorimetry (DSC), thermomechanical analysis (TMA), and thermogravimetric analysis (TGA). Furthermore, we explore optical properties through tests on birefringence, UV-VIS spectroscopy, and haze measurements. Particularly, testing polymers at high temperatures can provide crucial engineering design criteria for producing protective films for batteries, which is significant given the rising risks of electric vehicle fires. This contributes to the safety of society and humanity. Since various industries require both deep knowledge of materials and an understanding of processes, we, as mechanical engineers who comprehend manufacturing processes and are versed in polymer physics through diverse experiences with polymers and materials, are well-suited for this field.
- Keywords: polymer blends, PP/PE films, fire retardants, polymer characterizations
02. Debond-on-demand adhesives for electric vehicles
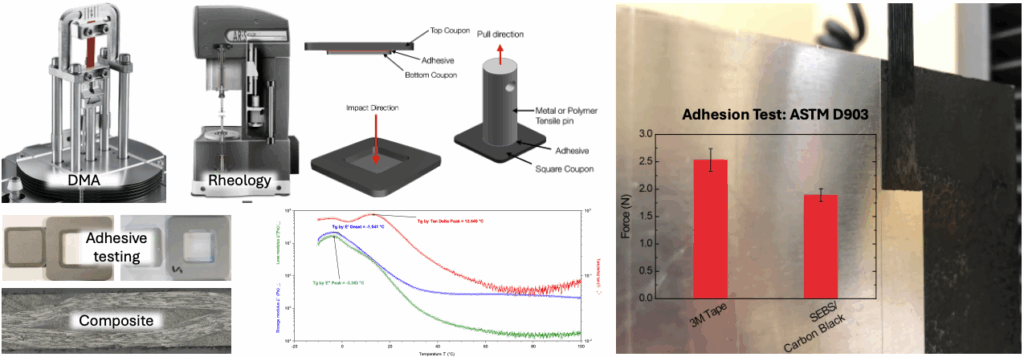
With the commercialization of electric vehicles, environmental issues arising from waste batteries have emerged, highlighting the importance of waste battery recycling technology. However, electric vehicle batteries are firmly fixed to the vehicle structure with adhesives, making their removal difficult. To address this problem, debond-on-demand technology—which allows adhesives to be separated at the desired time—is being applied to adhesives. While methods that apply heat are generally used, batteries are vulnerable to heat and are bulky and heavy, so mechanical or electrical methods are being considered. In this study, we research debond-on-demand adhesives for automotive battery recycling, aiming for commercialization through process optimization.
- Keywords: debone-on-demand, adhesive, PSA, epoxy, electric vehicle, sustainability, battery recycle
01. Structure-property relations established using computations (DFT, molecular dynamics, machine learning)
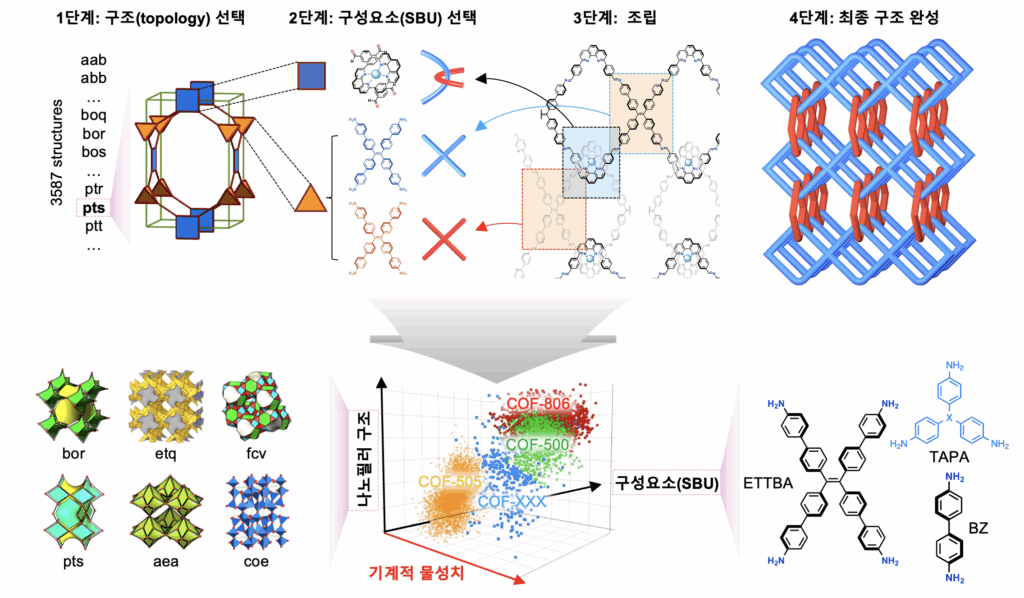
This research aims to compile mechanical property data of crystal structures using molecular dynamics (MD) simulations and employ machine learning to develop an AI-based tool for crystal structure design and engineering. The AI tool will select appropriate topologies and secondary building units (SBUs) based on mechanical properties. By performing MD simulations on unit cells with minimal atom counts under static conditions (eliminating the time variable), we can accelerate calculations and accurately obtain mechanical properties, such as stiffness, without surface effects. The method involves applying strain to the periodic boundary condition (PBC) box to analyze tensile/compression and normal/shear behaviors, and conducting molecular statics simulations to study crack propagation, dislocations, relaxation, defect energetics, and modulus. We will provide a “COF Database” containing mechanical property information for various topologies (up to 2,495) and SBUs (up to 279), encompassing millions of combinations, including 5,856 two-dimensional and 262,831 three-dimensional structures, along with properties like mass density, accessible surface area, pore fraction, and other mechanical properties. The force field creation process involves four steps: First, selecting the appropriate topology from the RCSR (rcsr.net) library. Second, generating structures and potentials for individual building block units using tools like LigParGen, which automatically creates force fields for organic molecules or ligands. Third, assembling the building units into the selected topology without bonding them. Finally, forming the final structure by bonding the building units together.
- Keywords: crystal structures, molecular dynamics, force fields, topology, mechanical properties
Biomaterials
03. Programmable fluid flow
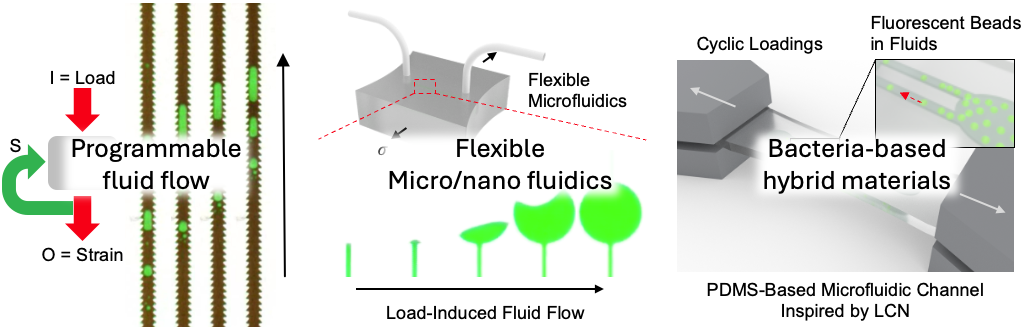
When mechanical loads are applied to bone, they cause deformation of the bone matrix, creating pressure gradients within the lacunar-canalicular network—a microscopic system of channels and spaces housing osteocytes. This pressure gradient drives interstitial fluid flow through the canaliculi and lacunae. The movement of fluid exerts shear stress on the membranes of osteocytes, stimulating mechanosensitive cellular responses. Thus, load-induced fluid flow within the lacunar-canalicular network activates osteocytes and plays a crucial role in mechanotransduction, initiating signals that regulate bone remodeling and adaptation. We used this interesting fluidic behaviors induced by mechanical loading applying flexible microfluidic devices.
- Keywords: load-induced fluid flow, bone, programmable flow, microfluidics, particle transport, surface tension
02. Dragonfly wings
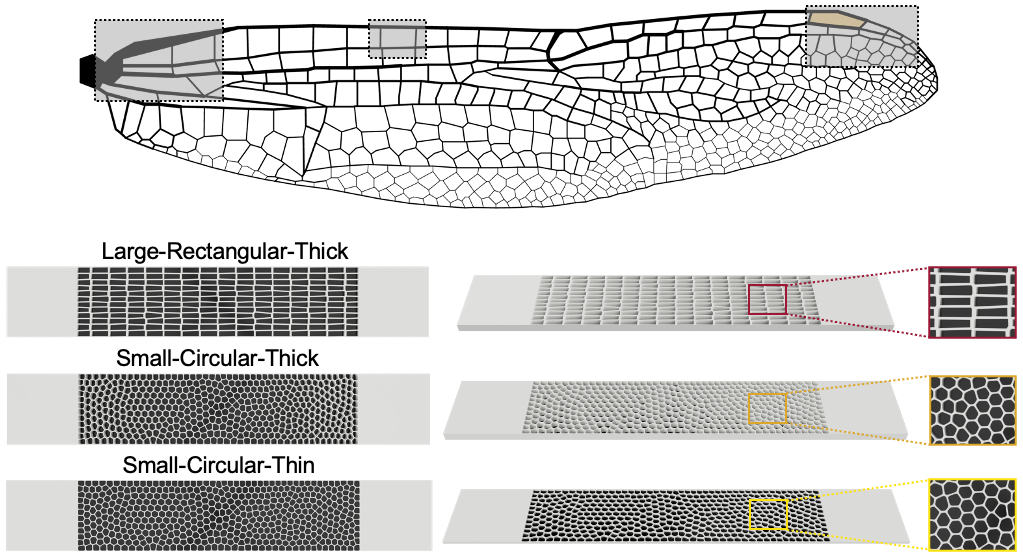
Flapping robot wings are inspired by nature and designed with composite structures. However, the previously reported robot wings are relatively monotonous compared to the real wings found in nature. In the case of dragonfly, its wing has a unique feature but shows statistical tendencies with geometrical parameters, such as vein thickness, circularity, and domain area. And these parameters dominate the rigidities of the cellular structures. Here, we compared the mechanical rigidity and ductility of different cellular geometries found in dragonfly wings based on experimental and computational results. The different mechanical properties governed by the vein structure results in different fracture behaviors. Therefore, the wing designs can be optimized based on structure-mechanical property relations to achieve the improved mechanical stability and aerodynamics characteristics.
- Keywords: flapping robots, nature-inspired designs, dragonfly, fracture, mechanical flexibility, 3d printing
01. Beeswax luminaires
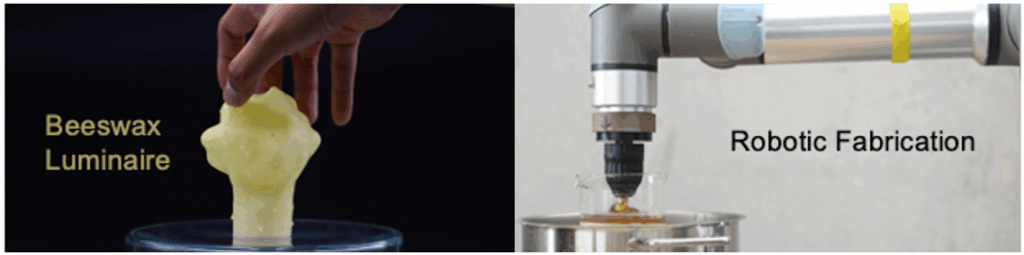
Biogenic materials are essential for sustainable manufacturing to reduce environmental footprints. This study proposes the “Beeswax Luminaires”, a user-friendly, non-toxic, and customizable production technique for designing with waxes. Beeswax Luminaires utilize naturally sourced materials—water and beeswax—to achieve a more sustainable lighting solution. They are designed through a multi-disciplinary collaboration involving materials science, computational design, and robotic fabrication. Chemical, thermal and mechanical properties of beeswax are characterized prior to the design and fabrication processes. Parametric modeling is used to create optimized designs and an adaptable production flow. Robotically fabricated samples of two designs are compared for defects, compressive strength, and light diffusion. By understanding the physical properties of beeswax and incorporating digital modeling and fabrication, Beeswax Luminaires achieve optimization, scalability, and sustainability in design and manufacturing.
- Keywords: beeswax, biomaterials, lighting design, computational design, robotic fabrication, sustainability